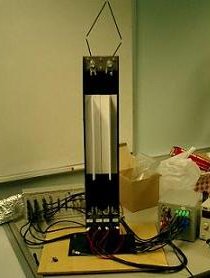
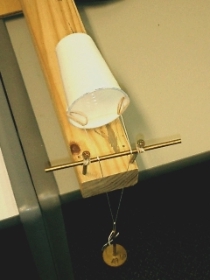
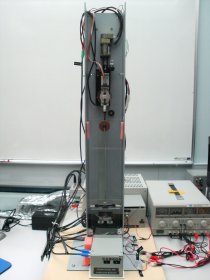
People
Project Team:
- Yee Harn Teh
- Roy Featherstone
- Laura Hege (visitor)
- Sylvain Toru (visitor)
Partners:
- Zbigniew Stachurski
Project Description
Actuators based on shape memory alloys (SMA) can be small, simple, cheap, clean, silent, and have high force-to-weight ratios; but they also have disadvantages, including low efficiency, low speed and low accuracy. This project aimed to improve the speed and accuracy of these actuators, by developing better feedback control systems, so that they can be more widely used in robots, medical devices, consumer electronics, and so on.
We chose to focus on actuators that use antagonistic pairs of Flexinol® wires (available from Dynalloy), which are made of a nickel-titanium SMA called nitinol. These wires can be stretched easily when cool, but contract forcibly to their original length when heated. The heating can be done simply by passing an electric current through the wires.
So the big challenge in this project was to develop control systems that deliver fast and accurate tracking of force and motion command signals by passing the right amount of current through the wires. This is not easy because SMAs exhibit highly nonlinear behaviour, including substantial hysteresis, which makes them very difficult to control. To see what we achieved, take a look at the talks section below.
Results
-
We invented a new rapid heating algorithm that roughly doubles
the speed of SMA actuators while also protecting them from being
overheated. We have two movies showing the rapid heating
algorithm at work:
- movie 1. This movie shows the pantograph robot tracking a square at speeds of up to 1Hz, using Grant's relay controller (see publication 1) augmented with our rapid heating algorithm. The speed is very good, but the tracking accuracy is poor.
- movie 2. This movie shows the step response and tracking response of a new motion control system (see publication 8) with and without the rapid heating algorithm.
- We showed that SMA wires can respond at frequencies of 1kHz and higher, by building an SMA loudspeaker. Yes, SMA really can respond at audio frequencies, and here is the audio to prove it!
- We obtained a gain/phase model of the high-frequency dynamics of nitinol SMA wires. According to this model, the heating-power to force transfer function is a first-order low-pass filter in which the gain varies slightly with mean stress and strain on the wire, but the phase response is invariant. (See publications 7 and 9.)
- We developed a force control system with a slew rate of 50N/s and an accuracy better than 1mN in a +/−3N range. (See publications 8 and 9.)
- We developed a fast, accurate stiffness control system, which makes the actuator behave like a programmable spring. (See publication 10.) At low commanded stiffnesses, the performance of this controller is almost as good as the force controller.
Publications
- Y. H. Teh 2003. A Control System for Achieving Rapid Controlled Motions From Shape Memory Alloy (SMA) Actuator Wires. B.Eng. Honours Thesis, Dept. Engineering, The Australian National University. Full Text.
- R. Featherstone & Y. H. Teh 2004. Improving the Speed of Shape Memory Alloy Actuators by Faster Electrical Heating. Int. Symp. Experimental Robotics, Singapore, 18–21 June 2004. Full Text. Slides.
- Y. H. Teh & R. Featherstone 2004. A New Control System for Fast Motion Control of SMA Actuator Wires. Shape Memory And Related Technologies (SMART 2004), Singapore, 24–26 November 2004. Full Text. Slides (powerpoint).
- Y. H. Teh & R. Featherstone 2004. Experiments on the Performance of a 2-DOF Pantograph Robot Actuated by Shape Memory Alloy Wires. Australasian Conf. Robotics and Automation (ACRA 2004), Canberra, Australia, 6-8 December 2004. Full Text.
- Y. H. Teh & R. Featherstone 2005. Experiments on the Audio Frequency Response of Shape Memory Alloy Actuators. Australasian Conf. Robotics and Automation (ACRA 2005), Sydney, Australia, 5–7 December 2005. Full Text.
- Y. H. Teh & R. Featherstone 2007. Accurate Force Control and Motion Disturbance Rejection for Shape Memory Alloy Actuators. IEEE Int. Conf. Robotics and Automation, Rome, Italy, 10–14 April, pp. 4454–4459. DOI. (Note: the SMA model shown in this paper is not correct. The correct model appears in publications 7 and 9.)
- Y. H. Teh & R. Featherstone 2007. Frequency Response Analysis of Shape Memory Alloy Actuators. Int. Conf. Smart Materials and Nanotechnology in Engineering (SMN 2007), Harbin, China, 1-4 July. Also in Proc. SPIE vol. 6423, p. J4232, 2007. Full Text.
- Y. H. Teh & R. Featherstone 2008. An Architecture for Fast and Accurate Control of Shape Memory Alloy Actuators. Int. J. Robotics Research, vol. 27, no. 5, pp. 595–611. DOI. Full Text.
- Y. H. Teh 2008. Fast, Accurate Force and Position Control of Shape Memory Alloy Actuators. Ph.D. Thesis, Dept. Information Engineering, The Australian National University. Full Text.
- S. Toru 2008. Fast and Accurate Position Control of Shape Memory Alloy Actuators. Research Internship Report, Dept. Information Engineering, The Australian National University. Full Text.
Talks
- Seminar: High Performance Force Control for Shape Memory Alloy (SMA) Actuators
- Achieving High Performance from SMA Actuators. 2011. (30 min) Abstract. Slides. Slides X4. Presented at the IEEE ICRA 2011 Workshop on Biologically-Inspired Actuation.
Note: the slides contain references to Roy's old URL at the ANU, which is obsolete.
Conclusion
This project was active from 2003 to 2008. In that time, we developed an entirely new force control system that achieved both excellent speed and ground-breaking accuracy. Furthermore, it achieved this level of performance while simultaneously protecting the SMA wires from overheating and from mechanical overload. We also had a bit of fun with the SMA loudspeaker; and we developed a stiffness controller that was almost as good as the force controller. However, our position controllers were either fast but inaccurate, or accurate but slow. Many interesting ideas were developed during the course of this project, which have had an influence on subsequent research and development.